Living on the Edge: How Embedded Edge Computing Devices can Help Industrial Producers Do More with Digital Transformation
December 05, 2023
Blog
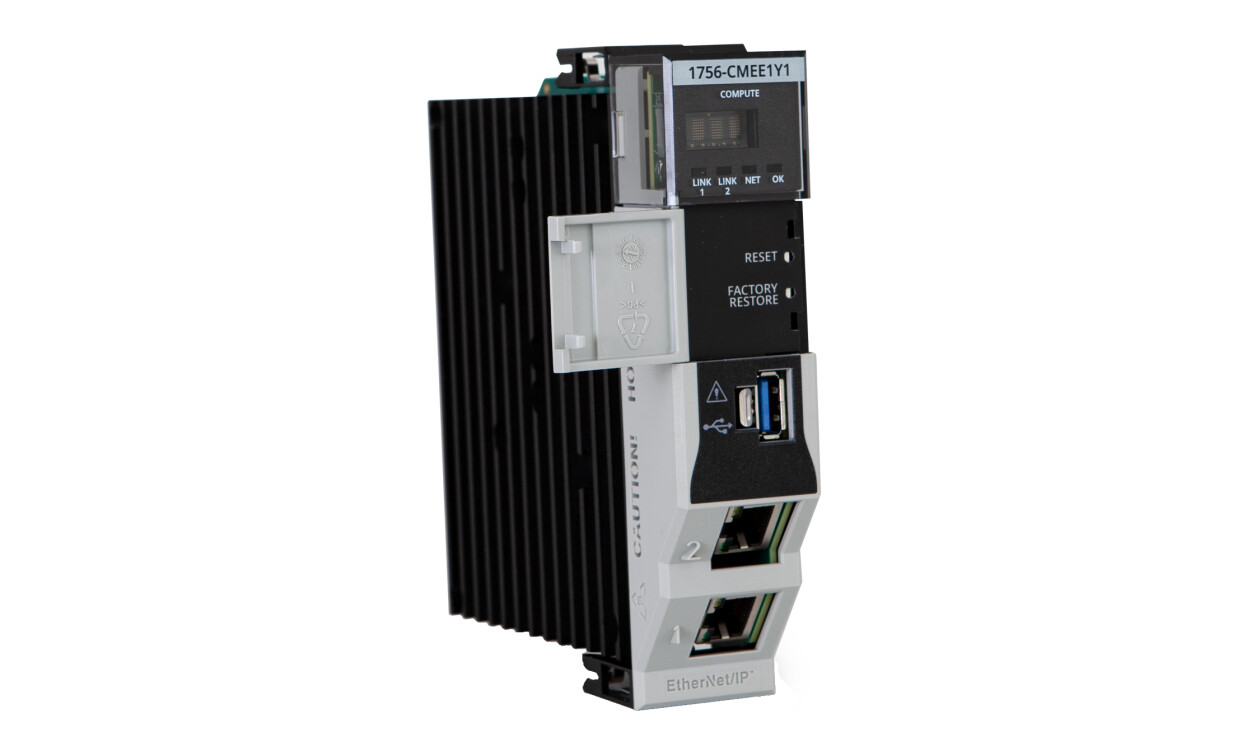
Digital technology and connectivity are creating not only new possibilities in industrial operations, but also ever-growing volumes of data. For practical, financial, and security reasons, industrial producers can’t just send all this data to the cloud. They need to keep some of it close to where it’s produced – at the industrial edge.
This is helping drive the adoption of embedded edge computing. These computing devices, deployed next to or even as part of an industrial control system, can facilitate real-time data processing for time-sensitive production applications. They also enable new and better ways to use technologies like advanced analytics, artificial intelligence (AI) and robotics that can transform how industrial producers compete. And the devices can reduce cloud data bandwidth and costs.
From a security standpoint, embedded edge computing can give industrial producers peace of mind that their sensitive or confidential data is being contained or processed on-site, near where it’s produced. The devices also help producers comply with data-privacy regulations that dictate rules for data communications and storage.
Embedded edge computing brings IT/OT convergence to the controller level. But, with the right strategy, these computing assets can navigate some of the complexities of IT/OT convergence on their own, so designers and end users can instead focus on unlocking the most value from the devices in their applications.
Get more value from data at its source
Because embedded edge computing devices are deployed close to where data is produced, they have a low network latency and as a result can provide real-time data. This makes them ideal for optimizing time-sensitive applications where mere milliseconds matter.
For some production processes, variables like current, pressure, or speed may need to stay within very tight thresholds for quality purposes. An embedded edge computing asset can monitor those variables with a high degree of accuracy to help maintain a desired quality level.
Similarly, predictive maintenance applications require software to constantly monitor a machine’s operations and detect deviations from its baseline performance. But those deviations may be just the slightest increase in vibration, current, or something else.
Using an edge-based application to track a machine’s performance and diagnostics in real-time can help detect issues earlier than a cloud-based application might detect them. This can give technicians more time to address issues before they cause unplanned downtime.
Embedded edge computing devices can also enable modern robot applications
Increasingly, robots aren’t being confined to walls or fixed tracks like in the past. They’re mobile. And they’re using computer-based vision and positioning capabilities to handle and move materials around on the production floor, while avoiding people and other assets around them. Embedded edge computing can put the computing asset in a robot, next to its controller, to support its safe and effective operation.
Data-intensive applications.
AI-driven quality inspections, for example, can help optimize quality while reducing demands put on today’s constrained production workforce. The AI-based system can continually monitor for quality variations and either recommend process adjustments to operators or trigger those changes itself with closed-loop quality control. And if the application runs on an embedded computing asset at the edge, quality changes can be made near instantaneously.
Embedded edge computing can also help facilitate more flexible lot-of-one production models. Driven by e-commerce, many manufacturers are seeking to offer more customized, even personalized products. But to do this, they need smarter, more flexible machines that can efficiently and accurately change over for each new product.
Embedded edge computing devices can be a key enabler of these machines, managing processes from inputting settings for each new production run to monitoring and reporting the quality of finished products.
Considerations for deploying
Choosing the right embedded edge computing solution can help set up both machine designers and end users for success.
For instance, pushing digital transformation initiatives to the industrial edge can create work – like the need to integrate data from multiple technologies and build custom applications. But some embedded edge computing devices help reduce this work.
A good example is a device that offers a wide range of connectivity options, like providing communication paths to REST API, OPC UA, and MQTT protocols. This helps facilitate IT and OT interoperability and comprehensive data exchange between the edge compute device and other technologies.
Some embedded edge computing devices are also designed to use pre-built applications. A pre-built visualization application, for instance, allows engineers to deploy customizable dashboards and analytics for their machines without needing to write a single line of code. Pre-built remote-access applications can also be used with the computing devices, making it easy for experts and technicians to monitor and help troubleshoot machines from remote locations.
Engineers can also choose from a variety of embedded computing technologies to meet their unique needs. For a greenfield facility, or a new line in an existing facility, they may want to use an industrial controller that already has a computing asset built in. But, if they’re adding the computing device to an existing line, they may opt for an embedded edge computing module that can simply be added to the same rack as the controller.
A module can also be used to add applications like analytics in regulated industries like life sciences. In an instance like this, the module isn’t changing the controller’s function, so the application doesn’t need to be revalidated.
Regardless of what edge devices are chosen, they should be deployed with a strategy that prioritizes security, simplicity, and scalability. Cloud-based edge management software makes that possible. It can help end users more easily manage edge devices from provisioning devices, with one touch, to having a single view into all edge devices deployed across the enterprise and every application installed on them. The software can also help strengthen security by configuring security profiles, firewalls, and user access across edge devices.
Complementary technologies
The question isn’t if, but how, a scalable computing approach that combines cloud and edge technologies will help industrial producers. Cloud computing will continue to be the workhorse for smart manufacturing applications because it offers centralized storage and scalable processing power. But embedding computing assets at the edge can also deliver significant value by creating more responsive machines, managing data-intensive applications, and keeping data contained to local assets.