5 Misconceptions About Test Equipment Obsolescence
August 16, 2023
Blog
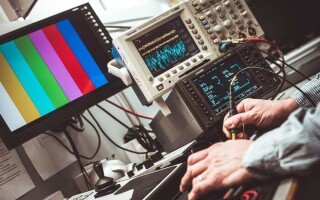
While the term obsolescence often brings to mind equipment that is decades old, the truth is that advancements in technology can quickly render even relatively new hardware obsolete.
1. Obsolescence Only Impacts Older Equipment
The global transition from analog to digital technology has been marked by the widespread adoption of the internet, which has connected the world like never before. Thanks to the instant access to vast amounts of information and open-source coding resources that the internet provides, companies compete to remain at the forefront of technological innovation. This global competition can render some hardware obsolete within only a few years.
The rapid advancement of technology is evident in semiconductor chips. Coined in 1965, Moore’s Law asserts that the number of transistors in digital semiconductor chips doubles every two years while the price halves. With more transistors, chips become faster, more powerful, and more energy-efficient. Digital semiconductor chips had around 3,000 transistors in 1970, whereas chips today have over 5 billion transistors. While this law has held for several decades and remains relevant today, the technological landscape continues to grow even more complex with the introduction of new technologies.
2. Obsolescence Only Affects Certain Industries
Test equipment obsolescence impacts any industry where test and measurement are essential to the design, production, and maintenance of systems and products — meaning that test equipment obsolescence impacts virtually every industry including the electronics/semiconductor, aerospace, defense, telecommunications, automotive, medical/healthcare, industrial manufacturing/automation, transportation, and research industries.
Each one of these industries relies on test equipment for quality control, diagnostics, research, optimization, and more. If the production process of one industry is disrupted by obsolescence, it can negatively impact other sectors in the global supply chain. For many industries, obsolete test equipment incongruent with the system can result in health and safety concerns.
3. Obsolescence is Only a Technical Issue
Test equipment obsolescence involves more than just the hardware. It can also impact software, the availability of spare parts and support services, and the ability to calibrate systems.
Some manufacturers, such as NI, market their products with a “product lifecycle.” For NI specifically, there are six stages of a product’s lifecycle- Active, Mature, Last Time Buy, Standard Support, Limited Support, and Discontinued. These different stages also indicate different levels of availability for vital services such as calibration and repairs. The older a part gets, the less technical support is available, leaving users with little access to resources that help them troubleshoot issues.
As a result of obsolescence, companies can encounter higher maintenance costs, compatibility issues when integrating equipment or software, and longer downtimes.
4. Obsolescence Planning is Unnecessary
Test equipment obsolescence negatively affects companies that have no plan in place to address it. Lower efficiency, higher costs, slowdowns, or even complete shutdowns of production lines are all possible results of unaddressed obsolescence. For industries in the military sector, such as aerospace and defense, products are intentionally designed to be used and serviced for decades. Test engineers in these sectors have the additional challenge of working primarily with outdated technology that is particularly challenging to replace or update, making it all the more important to have a detailed plan.
5. Obsolescence is a One-Time Problem
As we have seen in the points above, obsolescence is anything but a one-time issue. As technology rapidly evolves, test equipment hardware that is standard today is at risk of becoming obsolete. It is incredibly beneficial for companies to take action now, developing a method to address obsolescence as part of their long-term planning.
There are manageable steps that companies can take to address the ongoing issue of obsolescence. One step would be to update the technology in their test system in increments instead of opting for a complete infrastructure redesign. This strategy allows for minimum downtime while gradually upgrading to new technology. PCI eXtensions for Instrumentation (PXI) hardware is common with this approach, as the modular design makes it easy to integrate updated modules one at a time. It is significantly simpler to replace the chassis and controller of a test system after replacing the modules.
Another beneficial step would be identifying and contacting companies that specialize in obsolete test equipment relevant to the company. Value-added resellers, such as Apex Waves, offer repair and calibration services for parts no longer available from the manufacturer. These companies can also provide much shorter lead times for ordering urgent part replacements to keep test systems running in the face of obsolescence.