Railway Data Collection Serves Train Protection and Monitoring, Amongst Other Traits
July 12, 2022
Sponsored Story
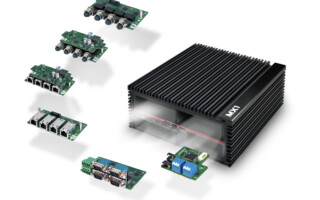
Trains continue to travel at higher speeds, go longer distances, and carry more passengers. Without the proper safeguards in place, these facts could result in a less than desirable situation.
For example, it’s not unusual to see trains approaching or even exceeding 200 miles/hour (MPH). Reaching those speeds in a way that is safe for passengers as well as people (and things) near the tracks is imperative.
As a result, more safeguards are being put in place to continuously monitor and protect the trains and provide early warning signals. One primary method of doing that is by adhering to the International Railway Industry Standard (IRIS) standard. IRIS is a global system for the evaluation of rail sector companies. There are more than 2000 certificates in place, with more coming on a regular basis. Oftentimes, the certificates are country-specific.
A typical train protection and monitoring system consists of a central signal monitoring embedded computer, a driver console, a recording unit that logs all activities occurring on the train, a digital speed indicator, and a balise (an electronic beacon or transponder that’s placed between the parallel rails).
Obtaining information from a high-speed train over a 5G connection is the best way to ensure the safety of the train and its passengers. The proper hardware-software combination allows for AI-based monitoring and analytics, and decisions that can occur in real time.
The central monitoring system, such as the MiCMS from MiTAC is used for power-supply detection, specifically looking for low voltages and relay-room or grid outages. It can also keep an eye on generator status, the track circuit and relay box door, and the railway crossing power supply. The MiCMS ties together all the hardware, software, and related sub-systems using a unified human-machine interface (HMI). Hence, it lets the system administrator gather all the necessary information and potentially control the train.
Keep the Pantographs Operating Properly for Maximum Safety
Pantographs are used to collect power information through contact with the railway catenary lines. This occurs using a suspended apparatus that’s mounted directly onto train’s roof. It’s vital to keep the pantographs in proper working order, as damage could result in delays and disruptions to the entire network. Pantograph arcing is a common and unavoidable phenomenon in electric trains, which can result in voltage surges and electromagnetic interference (EMI).
In some cases, train providers have resorted to artificial-intelligence (AI) techniques to detect when a pantograph has been damaged. Those same techniques can be used to quantify the amount of damage that’s been sustained. It does this using cameras both on the trains directly and others mounted at various locations, even while operating at high speeds. Note that the system must be smart enough to account for varying weather and lighting conditions and different operating speeds. And of course it must be able to handle the shock and vibration that a train exhibits.
5G Increases Data Throughput and Thereby, Train Safety
One of the keys to making all these leading-edge technologies operate cohesively is the ability to quickly send and receive large amounts of data. To that end, 5G has been a boon to all areas of safe and reliable train operation. That includes monitoring of the pantograph. In most cases, 5G allows decisions to be made in real time as data is continually flowing in and being processed, inferenced, and analyzed with levels of accuracy that were not previously realizable. A person either aboard the train or in a central location can be alerted should an action be necessary.
The MiTAC MX1 embedded computer system is powered by an Intel Coffee Lake Xeon or Core-i microprocessor. It has all the features needed to handle ATP and monitoring applications.
One system that’s capable of handling all the requirements of automated train protection (ATP) is MiTAC’s MX1-D rugged embedded computer platform in a fanless configuration. The heart of the MX1 is Intel’s Coffee Lake C246 workstation chipset that can support a Xeon or Core-i LGA1151 socket-type microprocessor to process real-time data. Combined with AI modules powered by Intel Movidius Myriad X, it delivers the performance to efficiently handle plate recognition. It boasts over-current and over-voltage protection and an expandable design that can grow as the requirements mature. Note that a similar platform, the MB1, is housed in a smaller form factor aluminum enclosure that is designed with Mini PCIe slots, and draws less power.
In terms of I/O, the MX1 is built with dual Ethernet ports, eight USB interfaces, a PCIe X16 slot, and various video outputs. There’s room for three 2.5-in. disk drives and two mPCIe slots for SSDs and wireless access. Depending on the configuration, the MX1 can operate from -40°C to +70°C and can withstand up to 50 Grms of vibration.
There are myriad reasons why an ATP producer would opt for the MiTAC solution. For example, the company complies with the EN50155, EN50121, and EN45545 certificates. The company’s products offer versatile expansion through Power-over-Ethernet (PoE) for camera connection, and can handle wide voltages and temperature ranges. 5G connectivity supports dual SIM cards to ensure good signal strength.
When it’s all said and done, passenger safety must be the top priority. Many of the pieces needed for ATP are available, and MiTAC assembles them in a neat, compact, package.