Melexis Improves Robot Functioning to Interact with Fragile Objects
April 07, 2022
Blog
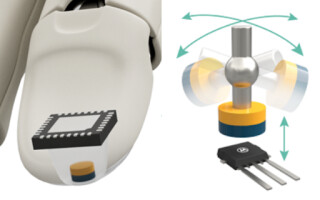
The highly compact tactile sensor features multiple 3D magnetometers through Melexis’ Trixaxis technology– protected against magnetic stray fields.
Improving the manufacturing of sensor assemblies and modules has always been the forte of Belgium-based robotic engineering manufacturer– Melexis. There is a need to comply with the industry standards and the increasing requirements for major innovation in transforming the way robots interact with fragile and delicate objects.
Leveraging the in-house and proven Triaxis technology, the semiconductor company introduces a tightly integrated and compact tactile sensor– Tactaxis [1]. With the small footprint, the tactile sensor aims to improve the robot's grip to handle diverse objects like fruit picking. There has been a series of evaluations and validation of the hardware to achieve successful implementation in a functioning prototype with a sense of credibility.
What makes the Tactaxis a Game Changer?
Taking a deep look inside the integrated tactile sensor, Tactaxis proclaims the key offering of multiple 3D magnetometer pixels, leveraged through the Triaxis technology, which will be discussed in more detail. Designed with a magnet embedded in the elastomer material gives the flexibility for soft contact interface– similar to human touch. Through the arrangement of various components onboard, the hardware is capable of detecting a small amount of force to generate relevant responses.
Magnetic sensors based around the Hall effect are only sensitive to the magnetic flux which is perpendicular to the surface of the Hall component [2]. Even after satisfying many applications, they still possess several challenges in design complexity and accuracy errors. To solve this, the magnetic Trixaxis sensor technology employs the integrated magnetic concentrator to provide three-axis magnetic field measurements from a standalone sensor IC. Increasing the custom ability of the sensor, the designed hardware is able to determine angular, linear, and 3D motion to output the individual magnetic components (in any preferred direction).
Minimalistic manufacturing measuring just 5x5x5 mm makes it a considerably good choice for space-constrained robots. Despite the size, the hardware has achieved a force resolution of 2.7mN which is more than enough to differentiate weight changes in a fraction of grams. The tight integration through cost reduction and improved sustainability proclaims volume production for the sensor in the near future. “By exploiting the capabilities of our Triaxis magnetic sensor technology, we have made a significant step forward in robot tactile sensors, providing a rugged and competitive multi-axis sensing solution,” explains Gael Close, Global Innovation Manager at Melexis.
As mentioned earlier, the gradiometric approach has made the Tactaxis immune to the magnetic stray field which is further explained in detail.
Tactile Sensor Immune to Stray Magnetic Fields
In the research paper, “A gradiometric magnetic force sensor immune to stray magnetic fields for robotic hands and grippers'' published under IEEE Robotics and Automation Letters, issue January 2022 [3], proposes a magnetic force sensor with multiple nearby pixels inside the same IC addressing the issue of stray fields generated from conductors, motors, and magnets. The researchers reutilize the MLX90372 Triaxis position sensor that outputs the angular displacement along the arc.
Tactile sensor immune to stray magnetic fields [Image Credit: Research Paper]
The gradiometric approach allows the sensor to prevent measurement errors despite the change in external parameters like temperature. To evaluate the prototype, innovators decided to deploy the tactile sensor on a commercial robotic hand to interact with a balloon. In the case of a single-pixel plain magnetometer, the force is regulated in the absence of stray-field disturbance. However, as the magnet approaches the hardware setup, the sensor is corrupted by the stray field, resulting in the robotic hand to either releasing or crushing the balloon. For the proposed methodology of multi-pixel, the sensor is not disturbed by the approaching magnet as the force of the robotic hand remains regulated. The experiment is demonstrated in the video published here.
We have witnessed an upward trend for improving robotic functioning in various resource-constrained areas. This new release will help several robot engineering manufacturers to effectively deploy the hardware with ease– reducing the time to market.
References
[1] Melexis, “Melexis gives robots a sense of touch,” Feb. 2022. Accessed: Feb. 10, 2022. [Online]. Available: https://www.melexis.com/en/news/2022/8feb2022-melexis-gives-robots-a-sense-of-touch
[2] Melexis, “Triaxis: Unique sensing solution.” Accessed: Feb. 10, 2022. [Online]. Available: https://www.melexis.com/en/tech-talks/triaxis-position-sensing-solution
[3] T. Le Signor, N. Dupré and G. F. Close, "A Gradiometric Magnetic Force Sensor Immune to Stray Magnetic Fields for Robotic Hands and Grippers," in IEEE Robotics and Automation Letters, vol. 7, no. 2, pp. 3070-3076, April 2022, doi: 10.1109/LRA.2022.3146507.